ソニハルのメーカーである英国NRG Marine社では、オフショア企業 OES Groupと協力して洋上風力タービンのメーカーとオペレータに建造および運用コスト削減の面で新たなソリューションを提供しています。
洋上風力タービンの多くは、その支柱の強度計算を行う際、海洋生物の付着に起因する流体力学的負荷を考慮して構造用鋼の厚さを増やす必要がありました。 ソニハルを使用することで、海洋生物の増殖を抑制、構造要件が軽減され設備投資が削減されました。 海洋生物の増殖は構造物の腐食の原因ともなるため、これまではオフショアの作業員ややダイバーによって定期的に清掃されていました。ソニハルによりこれら運用コストも削減できました。
さらに、はしごやステージなどに増殖した生物により滑りやすくなり、作業員の安全も脅かされる状況もありましたが、これも解決できました。
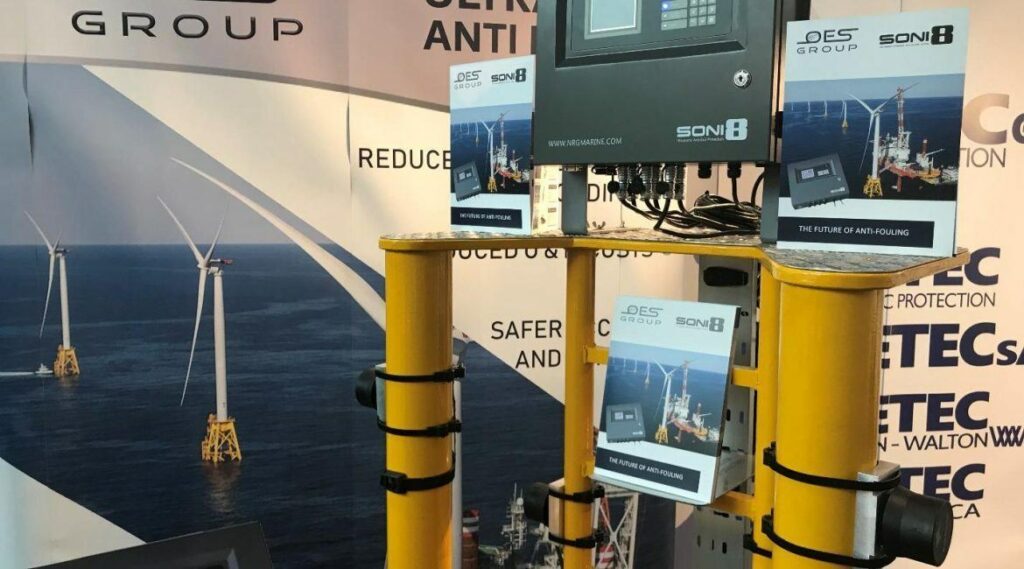
【原文】
Sonihull – Set to transform offshore energy sector
The world’s leading ultrasonic bio-fouling specialist is helping offshore windfarm engineers to reduce manufacturing costs, cut cleaning requirements and improve landing-stage safety.
NRG Marine, the UK-based manufacturer of Sonihull ultrasonic anti-fouling systems, in association with OES Group, has revealed a bold new future for manufacturers and operators of offshore wind turbines.
Sonihull ultrasonic anti-fouling systems are changing the way these offshore monoliths are being built and operated, providing substantial Capex and lifetime MRO savings.
“First, we have the design requirements for the foundations,” explained Dominic Findlow, Technical Director of NRG Marine, talking at WindEnergy expo in Hamburg. “In many cases, structural steel thickness has to be increased by 10% to account for the additional hydrodynamic loadings resulting from the attachment of marine growth. With an integrated Sonihull8 ultrasonic anti-fouling system we can control marine bio-fouling which will lower the capex for projects by reducing the structural steel requirements.”
“This weight-saving also reduces the initial installation costs. The absence of a thick carpet of marine growth will also save about 50 tonnes of added weight over the lifetime of an installation, which will reduce lifting costs again during decommissioning. Corrosion is also a key concern for these structures, marine fouling accounts for about 30% of lifecycle corrosion. So, keeping the fouling in check will allow operators to reduce the design burden here too.”
As with any marine-based structure, weeds and other bio-fouling will increase the hydrodynamic drag of an installation. To ensure that structural integrity is maintained even during very rough sea conditions, the weeds and fouling usually have to be maintained and regularly cut off by specialist offshore cleaning crews and divers.
“By integrating Sonihull8 systems into the underwater structures the build-up of weeds and other biofouling is reduced and this significant maintenance cost can be cut,” added Findlow. Another area that can cause serious problems is the landing-stage and ladder. Hard fouling will establish on the ladder areas which can be a safety hazard to service personally.
Softer growth will result in slipper ladder rungs which could also cause an injury during access and egress to the turbine. A Sonihull system fitted to the outer rungs and to the boat landing structure will prevent marine growth in this tidal area. The transducers benefit from an IP68 rating which also allows to be installed submerged if necessary.
No responses yet